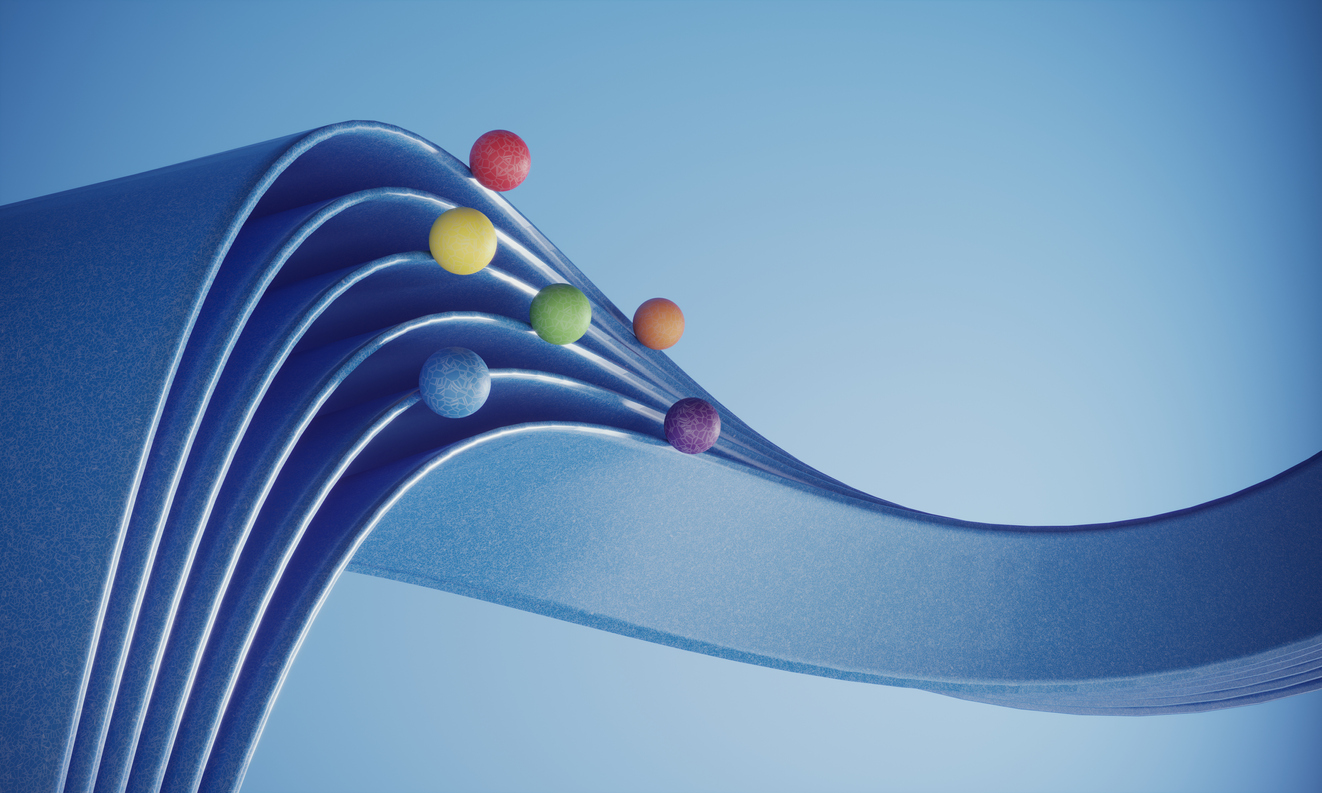
Meeting clinical need is only part of the equation for manufacturers pursuing Medicare reimbursement for durable medical equipment (DME). To qualify as DME under federal law, a product must also meet the minimum lifetime requirement (MLR). Per 42 CFR §414.202, items classified as DME on or after January 1, 2012, must have an expected life of at least three years.
This requirement is foundational to Medicare’s coverage determination process and serves as a key eligibility criterion for assigning a Healthcare Common Procedure Coding System (HCPCS) code. Understanding how the MLR is interpreted and applied by both the Centers for Medicare & Medicaid Services (CMS) and its contractors is essential for any manufacturer navigating the reimbursement landscape.
The Role of MLR in Coding and Reimbursement
The Pricing, Data Analysis, and Coding (PDAC) contractor, which performs HCPCS coding verifications on behalf of CMS, applies the MLR as a threshold criterion. When evaluating a request for a new or existing code, PDAC requires manufacturers to demonstrate that the product meets Medicare’s definition of DME, including its durability standard. Absent sufficient evidence, a product may be denied a code assignment—even if it offers meaningful clinical benefits.
The implications are significant. Without a HCPCS code, a product may be ineligible for Medicare coverage, reimbursement, or supplier billing. Because commercial insurers frequently model their own coverage and coding decisions after Medicare’s, failure to meet the MLR standard can have cascading effects, limiting provider adoption and patient access.
Demonstrating Durability Through Testing
Although CMS defines the MLR in regulatory terms, it has not issued detailed testing protocols. Manufacturers must, therefore, determine how best to document and demonstrate that a device can function for at least three years under expected conditions of use.
Durability testing strategies vary depending on the product’s design, function, and anticipated stressors. For example, a manual wheelchair might require testing focused on structural integrity under repetitive weight-bearing load, while a mechanical pump used with an external urinary catheter may warrant testing for vibration, impact resistance, and environmental aging.
Common testing approaches include:
- Vibration and Drop Testing
These simulate real-world handling conditions, such as repeated use, transportation, or accidental drops—key for products expected to be rented and reused by multiple beneficiaries.
Applicable standards include:- MIL-STD-810 (U.S. Department of Defense Test Method Standard)
- ASTM D5276-19 (Drop Test of Loaded Containers by Free Fall)
- ASTM D5487 (Simulated Drop by Shock Machines)
- Accelerated Aging
Also known as shelf-life testing, this approach estimates a product’s functional lifespan by subjecting it to elevated temperature and humidity in a controlled chamber. Standards such as ASTM F1980-21 provide guidance on accelerated aging for medical devices.
- Computer Modeling and Simulation (CM&S)
Manufacturers may also use computational tools for virtual durability testing. As defined by one of several modeling software companies, finite element modeling (FEM) simulates how a structure responds to stress by dividing it into smaller elements for analysis. Another virtual model, computational fluid dynamics (CFD) is used to evaluate how air or liquid movement can affect a device’s performance over time through models of pressure, temperature, and mechanical force.
- Custom In-House Testing
Manufacturers may also develop proprietary tests tailored to the product. These must be accompanied by a rationale explaining how the testing approach replicates real-world conditions and demonstrates three-year durability.
Supporting Documentation
Regardless of the testing method, manufacturers should compile a detailed report that outlines the testing rationale, methodology, results, and conclusions. The report should indicate whether the product meets the three-year minimum requirement and explain how that conclusion was reached. This documentation plays a critical role in PDAC’s evaluation and is often the deciding factor in whether a code is assigned.
Strategic Considerations for Manufacturers
The MLR should be viewed not just as a compliance requirement but as a critical point of strategic planning. Failure to anticipate CMS or PDAC’s evidentiary expectations can lead to delayed coding decisions, costly redesigns, or restricted market access.
Manufacturers that integrate durability testing early in product development—and align it with likely regulatory review—are better positioned to secure timely HCPCS code assignments and reimbursement support. In a landscape where product adoption often hinges on coding and coverage, documenting and demonstrating durability is not just advisable—it is essential.